WoodEye: эффективная оценка пиломатериалов
Новый сканер – для завода «Лесобалт»
На заводе «Лесобалт» установлен самый современный сканер для оценки качества ламелей. Даже несмотря на неблагоприятные прогнозы относительно будущего калининградского предприятия, обусловленные проблемами с сырьевым обеспечением из-за роста тарифов на транзитные перевозки и прекращения государственных субсидий, по применяемым технологиям и парку оборудования предприятие может дать фору многим отечественным и зарубежным заводам.
Высокое качество выпускаемой продукции подтверждается сертификатом немецкого института оконных технологий IFT Rosenheim, соответствует нидерландскому стандарту KOMO, а ответственное лесопользование осуществляется согласно нормам FSC. Несмотря на достижения в области качества, на заводе постоянно совершенствуются технологические процессы и повышается эффективность использования древесины.
Последовательная работа

Завод ориентирован на выпуск столярно-строительных изделий. Клееные оконные бруски, мебельный щит и погонажные материалы – основные виды продукции. За год на заводе перерабатывается около 120 тыс. м3 круглых лесоматериалов. Суммарный объем выпускаемой продукции около 30 тыс. м3.
На заводе заботятся о повышении эффективности использования сырья в производстве, что невозможно без внедрения современных способов контроля, позволяющих комплексно оценивать качественные характеристики предметов труда на всех участках.
Одной из наиболее ответственных операций, от точности выполнения которой в первую очередь зависит коэффициент использования сырья и качество выпускаемой продукции, является оценка качественных характеристик пиломатериалов. Все недопустимые пороки должны быть локализованы и вырезаны с минимальными потерями чистой древесины. Для оценки качества пиломатериалов на заводе применяются оптические сканеры WoodEye.
Первый сканер WoodEye для оценки качества ламелей из ангарской сосны и сибирской лиственницы был установлен на заводе «Лесобалт» в 2008 году. К тому времени завод, пуск которого состоялся летом 2005 года, производил около 1000 м3 оконного бруска в месяц, а сортировку пиломатериалов операторы выполняли вручную, работая в три смены, по 25 человек каждая. Поскольку завод ориентирован на поставки продукции в европейские страны, а также на продажи в России, операторам приходилось учитывать сразу несколько нормативов: российские стандарты, рекомендации института IFT Rosenheim, дополнительные требования к порокам древесины, прописанные заказчиками в технических условиях. Из-за большого количества контролируемых параметров работа тормозилась, возникали ошибки при классификации ламелей и усложнялся учет размерно-качественных характеристик и объемов продукции.
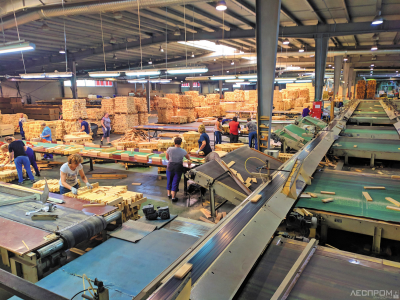
Низкая производительность при оценке качества пиломатериалов и использование ручной торцовки для вырезки дефектов по меткам операторов сдерживали развитие завода. Кроме того, часть деловой древесины попадала в отходы, поскольку при ручной разметке пиломатериалов невозможно точно очертить дефект. Эти ограничения предопределили необходимость инвестирования в развитие участка оптимизации пиломатериалов. В результате реконструкции 2008 года в деревообрабатывающем цехе были установлены два автоматических оптических сканера WoodEye четвертого поколения. Скорость оценки ламелей составила 120 м/мин, то есть примерно 60 тыс. пог. м пиломатериалов за смену, а для вырезки дефектов были приобретены две торцовочные установки OptiCut 350. Все это позволило уменьшить число операторов в смене до 14 человек, а также повысить производительность участка в 3,5 раза – до 3500 м3 пиломатериалов в месяц.
Результаты оценки ламелей не только передаются на станки OptiCut 350, но и отображаются на сенсорном экране, что позволяет операторам постоянно контролировать работу оборудования и наблюдать за выявлением дефектов и выполнением оптимизационной программы.
За 11 лет работы сканера, помимо регламентных работ, проводилось только обновление программного обеспечения – новые версии способствовали использованию оборудования с большей эффективностью за счет идентификации дополнительных пороков и выявления дефектов небольшого размера.
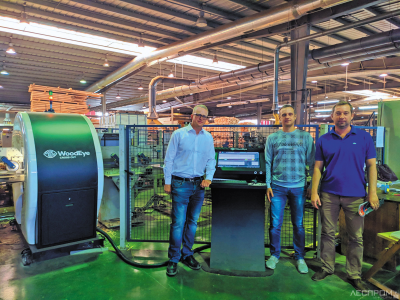
О принципиальном обновлении участка оценки качества ламелей на предприятии задумались в 2018 году, когда на заводе решили диверсифицировать производство и начать выпуск оконных блоков и мебельного щита из древесины дуба, закупаемой в Краснодарском крае и Воронежской области, а также расширить географию поставок. Выход на рынок Нидерландов потребовал сертификации предприятия по стандарту KOMO, который предъявляет более жесткие требования к клееным брускам. Так, например, в наружных слоях клееных брусков не допускается использование древесины с широкими годичными слоями, а также регламентируется наклон волокон в ламелях.
В 2018 году участок оптимизации пиломатериалов модернизировали. На одном из двух сканеров заменили ряд датчиков и усовершенствовали систему освещения. Для обслуживания второй линии оптимизации, на которой планировалось преимущественно перерабатывать лиственные пиломатериалы, сканер заменили самым современным в линейке WoodEye шестого поколения. В его конструкции использованы новые сенсорные системы сканирования, позволяющие осуществлять сортировку хвойной и лиственной древесины с учетом дополнительных критериев.
Установка дополнительной линии оптимизации обеспечила комплексную идентификацию характеристик древесины трех перерабатываемых предприятием пород и переход на двухсменный режим работы, а общее число операторов для обслуживания двух линий сократилось с четырнадцати до девяти.
Новые возможности
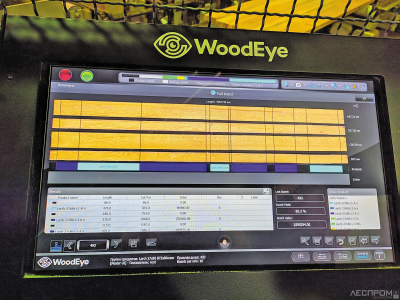
За счет использования новых моделей сенсоров и модернизации системы освещения сканер WoodEye шестого поколения не требует ежесменной калибровки по цвету, размерам и породе древесины. В результате увеличился коэффициент использования сканера, поскольку прежде на эти операции уходило до 15 минут рабочего времени в начале каждой смены и при поступлении другой породы древесины.
Помимо стандартного оборудования, новый сканер укомплектован лазерами, позволяющими обнаруживать даже мелкие трещины или чрезмерную шероховатость не только на пластях, но и на кромках ламелей, что важно при выпуске столярно-строительных изделий. Установленное программное обеспечение дает возможность корректно классифицировать такие сложные для оценки пороки, как синева, гниль, мелкие червоточины, а также местоположение заболони. Выбранную систему сканирования с дополнительным оборудованием при необходимости можно быстро перенастроить для оценки других пород древесины.
Индивидуальный подход
Новый сканер на заводе «Лесобалт» установили за два дня, но перед этим инженеры WoodEye кропотливо адаптировали программное обеспечение. Особое внимание было уделено распознаванию пороков и структуры древесины дуба, автоматизированная оценка которой отличается сложностью.
В соответствии с принятыми в компании WoodEye стандартами первичная настройка и оптимизация работы сканера проводились на заводе компании – производителя оборудования в Швеции, куда деревообрабатывающее предприятие направило образцы древесины с пороками. Цветовая гамма древесины даже одной породы может значительно различаться в зависимости от места произрастания, что необходимо учитывать при программировании оборудования. Дополнительные настройки при переходе на другие породы древесины можно внести и на деревообрабатывающем заводе заказчика, однако под некоторые породы необходимо изменить датчики, а это лучше сделать на станкостроительном предприятии WoodEye.
Одновременно с первичной настройкой на заводе WoodEye было организовано трехдневное обучение операторов. На занятиях также использовались образцы древесины, полученные от заказчика, а операторы научились выставлять и корректировать настройки оптимизации в соответствии с техническими условиями, принятыми на предприятии.
К следующему этапу оптимизации режимов работы сканера перешли уже после установки оборудования на деревообрабатывающем участке завода «Лесобалт».
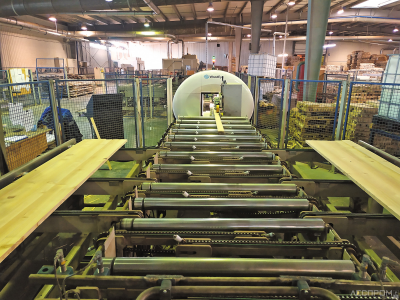
С первого дня на сканере не только выполнялась оптимизация пиломатериалов, но и создавался массив файлов с записью полных цифровых копий всех прошедших через него ламелей. С помощью таких файлов в специальной оптимизационной программе, поставляемой с оборудованием, моделировались варианты раскроя пиломатериалов на ламели при разных начальных условиях оптимизации. Такой подход позволил сформировать приоритеты, обеспечивающие максимальный объемный и стоимостной выход продукции с соблюдением всех ограничений по качеству древесины, указанных в технических условиях заказчиков и установленных применяемыми системами сертификации.
Поскольку у каждого клиента завода «Лесобалт» свои требования к качеству древесины, при оценке пиломатериалов с помощью математических алгоритмов выполняется расчет экономической эффективности возможных схем раскроя сортимента. Одни и те же пороки в ламелях по-разному влияют на стоимость продукции для разных заказчиков. Отказ от вырезки определенных пороков с получением ламелей большей длины может оказаться экономически выгоднее изготовления бездефектной, но короткомерной ламели.
На основе анализа результатов работы оптимизационной программы проводится заключительный этап настройки сканера. В дальнейшем, при изменении требований заказчиков, эту процедуру оператор сканера выполняет самостоятельно.
Постоянное повышение эффективности
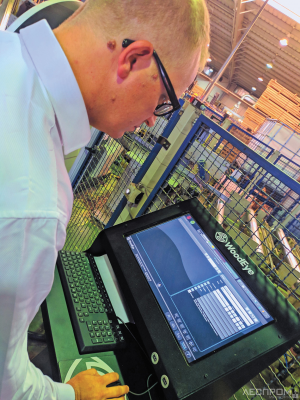
Несмотря на минимум два этапа настройки сканера, невозможно предусмотреть все необходимые сценарии работы оборудования, и периодически в них вносятся дополнительные ограничения. Большинство параметров работы линии оптимизации корректируется в интерактивном режиме. Одной из наиболее востребованных операций является изменение расстояния от границы дефекта до места его торцовки,
В зависимости от вида дефекта это расстояние подбирается таким образом, чтобы порок гарантированно не оказался в зоне шипового соединения, но при его удалении не приходилось захватывать слишком много полноценной древесины. В итоге обеспечивается экономия сырья.
Изменение подобных настроек согласно данным, получаемыми от сортировщиков на линии оптимизации, занимает до пяти минут.
По мнению руководителей предприятия, срок окупаемости инвестиций только за счет сокращения фонда оплаты труда операторов не превышает трех лет. Вместе с тем при установке подобного оценочного оборудования, кроме возврата вложений, обеспечивается высокая стабильность работы участка. Снижение влияния человеческого фактора, возможность быстрой настройки системы оценки дефектов при изменении требований заказчиков к качеству ламелей и повышение точности оценки дефектов до 98,5% в совокупности способствуют увеличению коэффициента использования линии и стоимостного выхода продукции, что в итоге повышает рентабельность участка.
Текст и фото Александр Тамби, д-р техн. наук, ассоциация «ЛЕСТЕХ»