Biele Group: «Мечтайте о большем!»
«Мы впервые приглашаем журналиста на производство, – говорит, пожимая мне руку при знакомстве, региональный менеджер Biele Group Андони Ириарте. – Тем более журналиста из России. Нет такого опыта, поэтому наш разговор будет своеобразным экспромтом». Что-то похожее я мог бы сказать и про себя: прежде на машиностроительных предприятиях в Испании бывать не приходилось, да и со Страной Басков знаком только по «Фиесте» Хемингуэя.
Тем приятнее было увидеть на входе в административно-производственный корпус завода Biele светящиеся на панорамном экране слова «Добро пожаловать, Максим Пирус, „ЛесПромИнформ“». Спасибо! Здравствуйте, приятно познакомиться! Что ж, давайте импровизировать.
Справка
Страна Басков (баск. Euskal Autonomia Erkidegoa, кратко Euskadi) – автономное сообщество на севере Испании, включающее три провинции: Алава, Бискайя, Гипускоа. Крупнейшие города: Бильбао, Витория-Гастейс, Доностия (Сан-Себастьян). Административный центр: Витория-Гастейс.
Официальные языки – баскский, испанский.
Баскония занимает восточную часть Кантабрийских (Баскских) гор высотой 1000–1500 м. Древенсые породы, представленные в лесах региона – дуб, каштан, бук и другие. Общая площадь дубовых лесов, предназначенных для вырубки, около 300 тыс. гектаров.
Площадь территории – 7234 км2. Население – 2189,5 тыс. чел. (2016 г.). Плотность населения – 302,67 чел./км2. ВВП на душу населения примерно 35,3 тыс. евро. Стремительный рост экономики в 80-х годах XX века превратил отсталый регион в богатый край с развитыми сельским хозяйством (животноводство и растениеводство; основные сельхозкультуры: пшеница, кукуруза, ячмень, овес, рожь и, конечно, виноград: Ла Риоха-Алавеса считается основным винодельческим районом испанского севера) и промышленностью: металлургической, металло- и деревообрабатывающей, бумажной, кожевенно-обувной, химической, пищевой.
Знакомство
«Чудесный народ эти баски», – писал классик. Портрет импозантного бородача в свитере (и да-да, это был Эрнест Хемингуэй, а вовсе не Эрнесто Гевара!) занимал почетное место на полке чуть ли не в каждой квартире Советского Союза на излете ХХ века – верить каждому его слову хотелось безоговорочно... Потому, даже по прошествии многих лет, перед вылетом в Бильбао в памяти моей неизбежно нарисовалась картинка: горы, кроваво-красная риоха в бокалах, бой быков, сдержанные, гордые люди с необъятным чувством собственного достоинства... С корридой в моей «индустриальной» поездке как-то не сложилось, а что касается соответствия реальности остальным ожиданиям – судите сами.
Компания Biele Group занимается разработкой средств автоматизации производственных процессов и линий для различных отраслей промышленности. В том числе – деревообрабатывающей, мебельной, плитной и особенно фанерной, что, по понятным причинам, составляло мой основной предмет интереса в поездке на два предприятия Biele Group.
В штате компании 300 сотрудников: более 200 на головном заводе в Аспейтиа и примерно 70 – на производстве Marzola. По 6 человек составляет персонал сервисных филиалов в США и Китае. Более половины сотрудников Biele Group – квалифицированные инженеры, специализирующиеся на высокотехнологичных решениях для крупнейших мировых корпораций и каждый раз находящие лучшие из возможных способов удовлетворения потребностей клиентов. Уровень клиентов Biele таков, что сами их имена могут служить рекомендацией. Оборудование Biele работает более чем в 50 странах, в числе которых Беларусь, Эстония, Латвия, Литва, Украина, Россия. Портфель заказов составляет около 60 млн евро: это примерно 25–35 крупных проектов ежегодно.
Слоган компании – Dream More («Мечтай о большем!») – как нельзя лучше соответствует всему, что говорят и делают здесь. «В чем же коренное отличие Biele от других фирм? Мы не стремимся продать клиентам то, что у нас есть, – говорит Андони Ириарте. – Мы делаем то, что клиент хочет, то, что нужно именно ему. Мы говорим: мечтайте о большем, мечтайте даже о несбыточном, а мы воплотим ваши мечты в жизнь. Идем от задачи: есть конкретная технологическая ситуация, совершенно индивидуальный запрос по выпуску конкретной продукции в определенных условиях, и его надо реализовать. Вопрос – как? Вот в этом и состоит наша работа: ответить на вопрос заказчика и доказать эффективность нашего решения делом».
Дивизион Biele Wood, согласно названию, специализируется на разработке и производстве автоматизированных систем для индустриальных процессов деревообработки: изготовления фанеры, прессования ламинированных панелей, обработки массива древесины и создания на его основе трехслойных клееных конструкций, облегченных и «сэндвич»-панелей, ДСП, окутывания древесных плит, изготовления напольных покрытий, мебели, дверного производства, производства волокнистых и композитных материалов, гипсокартона и других строительных материалов, упаковки. А также на модернизации существующих производств.
Отдельного упоминания заслуживают разработки компании для фанерной промышленности, охватывающие все этапы производства фанеры, начиная с обработки высушенного шпона: клеенанесение, обрезка, прессование, починка дефектов, шлифование и финишная отделка – покраска, облицовка и пр. «Тут важно не просто получить на выходе панель, – комментирует г-н Ириарте, – но и включить в процесс те стадии, которые повышают добавочную стоимость продукции, то есть создать ей товарный вид. И, разумеется, мы всегда можем интегрировать в линию участок упаковки».
«Многие российские производители фанеры, посетившие наше предприятие, были приятно удивлены не только бескомпромиссным качеством изготавливаемого оборудования, – говорит сотрудник компании Biele в России Сергей Зориков. – А еще и широтой применения его на фанерном производстве, богатством вариантов построения систем». Что касается упаковочных линий Biele, то они оказались весьма востребованными в мебельной индустрии. Например, концерн IKEA применяет их на своих предприятиях по всему миру, в том числе в России: на фабрике в Новгороде работают три линии – одна с ручным и две с автоматическим заполнением коробки.
Активное применение в производственных цепочках гидравлических прессов позволило компании достичь больших успехов в создании оборудования для выпуска ДСП, ЦСП, HPL и других плитных материалов, в том числе очень популярных сейчас пустотелых – с сотовым наполнителем. Двери и напольные покрытия, слоистые композитные и строительные материалы, резиновые, пластиковые и металлические детали – все это можно выпускать на машинах с логотипом Biele. И многое другое!
Как все начиналось
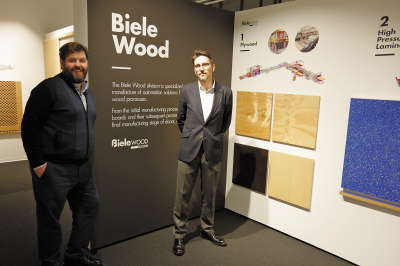
В 1973 году инженеры Хулиан Лацкано и Томас Летамендиа организовали совместную фирму по созданию и внедрению систем промышленной автоматизации и инжиниринговых решений для деревообрабатывающей промышленности. Поскольку фамилии обоих начинались на букву L, раздумывать над названием нового бизнеса долго не стали: пусть будет Biele – по-испански как раз так и произносится «двойное L».
1982 год – окрепший бизнес расширяется за счет привлечения капитала еще восьми партнеров, которые вместе с основателями образовали совет директоров Biele (члены их семей владеют компанией до сих пор).
Незадолго до десятилетия компания прошла акционирование: в 1982 году собственниками АО стали десять семей, представители которых изначально трудились в Biele . По сей день они и их потомки владеют компанией, а часть собственников продолжают в ней работать.
Через три года, в 1985-м, компания начала разработки для внедрения в металлургической и автомобильной промышленности, это расширение специализации привело к созданию в 1990 году трех профильных подразделений Biele: Biele Wood, Biele Metal и Biele Industrial.
1991 год – открытие новой производственной линии в г. Аспейтиа. Предприятие обрело новый дом, построенный с учетом нужд растущего производства.
1999 год – расширение нового завода, строительство нового цеха.
2004 год – компания удостоена премии PYME («Лучшая промышленная компания региона Гипускоа», в котором находится завод Biele). Этим званием работники очень гордятся и всячески стараются «держать планку».
2009 год – присоединение к Biele Group компании Marzola, производителя гидравлических промышленных прессов высокого давления. В результате этого стратегического слияния Biele Group получила возможность предлагать заказчикам уникальные проекты «под ключ» и комплексные решения, выстраивающие производственные процессы на промышленных предприятиях «от и до».
2015 год – в Атланте, штат Джорджия, создана дочерняя компания Biele USA, позволившая выйти за пределы Европы. Год спустя еще один сервисный дивизион – Biele CHINA пополнил ставшую международной группу.
2017 год – еще один шаг на пути к технологичному будущему: основано подразделение Biele Robotics & Artificial Vision для разработки и воплощения роботизированных решений и систем «искусственного зрения» (состоящих из видеокамер, сканеров, фотодатчиков и прочего и использующихся, например, на участках проверки качества для определения дефектов).
2018 год – принято решение о реорганизации Biele Group. Для обеспечения максимально эффективного обслуживания в компании выделены четыре направления: Biele Wood, Biele Metal, Biele Building и Biele Automotive.
«Компания создавалась с целью автоматизировать деревообрабатывающие производства, объединив в цепочки отдельно стоящие станки. Местность, где основан завод, отличается высокой концентрацией промышленных предприятий, в том числе дерево- и металлообрабатывающих. Поэтому основатели компании решили, что здесь на их работу будет спрос, – рассказывает Сергей Зориков. – Начинали с автоматизации техники других производителей (Burkle, Barberan, Homag, Steinemann и пр.), и до сих пор мы готовы по желанию клиента интегрировать любые станки в наши производственные линии.
А порой клиент хочет использовать в новой линии уже имеющийся у него станок, и мы интегрируем его в создаваемую систему.
Сейчас Biele выпускает полностью готовые участки собственного производства, однако есть виды оборудования, которыми мы не занимаемся, а при необходимости, выступая генеральным поставщиком, берем их у партнеров, – это шлифовальные, фрезерные и другие станки. Сотрудничество с ведущими машиностроительными компаниями отрасли позволяет Biele создавать любые конфигурации технологических линий, лучшие из возможных решений для деревообработки, металлообработки, производства строительных и иных материалов.
Как пример, полностью автоматизированная линия для шпонирования, реализующая последовательно несколько процессов: нанесение клея, прессование, фрезерование, шлифование и упаковку. Ее разработали и сделали мы, но в нее входят отдельные станки и агрегаты компаний-партнеров. Но какими бы узлами ни комплектовалась линия, ответственность за ее синхронизацию, общий функционал лежит на Biele. Контроль, управление, все ПО обеспечиваем мы. И делаем так, чтобы все это вместе работало с максимальной производительностью».
Экскурсия на два дня
Две основные производственные площадки Biele Group разделяют примерно 150 км, поэтому последовательное их посещение заняло у нас два полных дня. Первый визит – на «материнское» предприятие группы, ныне ставшее фактически ее штаб-квартирой.
Верхние этажи административно-производственного комплекса отданы «людям в белых халатах». Я не шучу: некоторые инженеры и проектировщики там одеваются именно так, что (по моему скромному мнению) подчеркивает как безукоризненную чистоту в помещениях, так и предельно уважительное отношение сотрудников к своим обязанностям. Впрочем, никаких жестких ограничений по униформе нет – другое дело, если вы собрались спуститься в цех: придется надеть специальную обувь, средства защиты и каску... которая выглядит как модная бейсболка.
Третий этаж занимает коммерческая служба. Инженеры-технологи готовят проекты совместно с ее работниками. Разработанное предложение попадает на стол технического директора (одного из хозяев компании) – он и сейчас изучает документы за панорамным окном своего кабинета. Соседний отведен руководителю службы управления проектами, а рядом размещается группа руководителей реализованных и реализуемых проектов: как только договор с клиентом заключен, назначается ответственный за проект. Понятно, в одиночку с проектом не справиться, поэтому руководитель собирает себе в помощь команду проектировщиков, которым поручено разработать всю линию с точки зрения механики, электрики, программного обеспечения. В общей сложности каждый большой проект ведет группа из 20–25 человек. Вертикальная структура совершенно прозрачна, система отчетности так выстроена и отработана, что совершенно не дает сбоев.
Отдел технического проектирования, помимо собственно проектирования, разрабатывает системы безопасности и электросхемы, готовит техническую документацию (в том числе инструкции по эксплуатации, каталог запчастей).
По неприметной лестнице спускаемся в большую комнату, где абсолютная тишина и даже воздух кажется стерильным. Это святая святых – тут работают программисты. Фактически это место, где обретает жизнь то «железо», что проектируется этажом выше. В штате компании около 25 программистов (это очень много, в иных компаниях всего два или три). По выбору клиента они могут адаптировать к своим разработкам элементы систем различных поставщиков: будь то продукция Siemens или Omron, Telemechanic или Allen-Bradley – в зависимости от предпочтений заказчика и задачи выберут и интегрируют в линию оптимальный вариант «электронной начинки». Всего на заводе компании трудится около 200 человек, 48% заняты на производственных линиях, 36% – это инженеры и конструкторы, 14% – сотрудники отдела продаж и поддержки клиентов, оставшиеся 2% – административные работники и руководство.
В заводском цеху никакой суеты. Каждый занят своим делом, но, в отличие от иных машиностроительных производств, это не бездушный конвейер-«потогон». Рабочий день на сборочном производстве составляет восемь часов с перерывом полтора часа на обед. Но, как отмечает Андони Ириарте, рабочие редко отдыхают больше часа: начинают в восемь утра, заканчивают к 17 часам. А вот при командировке на площадку клиента сотрудник Biele может работать 10 часов в день и даже больше – ведь специалисты понимают, насколько важно для заказчика как можно быстрее пустить оборудование в дело.
На заводе Biele осуществляется только сборка. Детали по чертежам инженеров компании отдел закупок заказывает на предприятиях партнеров.
«Мы не сверлим, не строгаем, не фрезеруем, – поясняет Андони Ириарте. – В 70–80 км от завода расположены малые и средние производители, которые берут на себя эти функции. Многие из них работают эксклюзивно для Biele, и, если посчитать их, то штат работников увеличился бы еще на сотню человек».
«Месяц от месяца картина на производстве меняется кардинально: сегодня, допустим, идет сборка линии для металлообрабатывающего производства, а некоторое время назад тут все было посвящено деревообработке и фанерному производству и на месте нынешней линии выгрузки деталей, оснащенной двумя роботами, располагалась линия форматной обрезки фанеры со шлифованием и автоматической загрузкой-выгрузкой, – рассказывает Сергей Зориков. – Сейчас она разобрана после тестирования и согласования с приемкой клиента, пакуется для отправки заказчику».
В отдельной стендовой зоне собирают и испытывают прототипы – именно тут впервые появляются новые узлы и машины, создаваемые по заявке клиента. Рядом с зоной сборки – стол с чертежами и списком ответственных за проект.
Любое изготовленное оборудование перед отгрузкой полностью собирается в тестовой зоне предприятия и пускается в работу. Только после тотальной проверки работоспособности и отладки режимов оно вновь разбирается до транспортной готовности и отправляется заказчику. Исключения из этого правила делаются только в тех случаях, когда клиент сам просит об этом. Тогда тщательное тестирование проводится на площадке клиента.
Все крупные проекты моделируются в трехмерном изображении, чтобы заказчик еще до воплощения техники в металле мог наглядно представить, какое оборудование он получит.
«Нужно отметить один очень важный момент: качество всего „железа“, – поясняет Сергей Зориков. – Кто бы ни приехал к нам на производство, непременно отмечает: да, на металле вы не экономите! Все добротное, крепкое, мощное, сделано на совесть – станины, профили, сварные швы, системы передач и иные компоненты систем».
Далее по ходу нашего движения – линия для мебельного производства (ее основной узел – 20-пролетный горячий пресс параллельно строится на площадке Marzola, а вся система автоматизации для линии, позволяющая с высокой скоростью подавать и разгружать пакеты, собирается здесь). В уголке готовится к монтажу будущая линия упаковки – собираются в близлежащей зоне детали, комплектующие, крепеж, инструменты. Каждый квадратный метр производства – работает.
В 1999 году производственные площади завода в Аспейтиа были существенно расширены, а сейчас одной из задач на перспективу поставлено их дальнейшее увеличение, продиктованное ростом числа заказов. Это стало возможным благодаря приобретению находящегося по соседству здания бывшей мебельной фабрики. Реконструкция и оснащение помещений начинается уже в текущем году. Это позволит нарастить производственные мощности и снизить сроки изготовления продукции, что, конечно же, делается в интересах клиентов.
Второе машиностроительное предприятие группы – Marzola расположено близ городка Логроньо, административного центра автономного сообщества и горного региона Риоха, издавна славящегося традициями виноделия. Вокруг огромное количество виноделен – только рядом с заводом их шесть. Вполне логично, что именно здесь в 1851 году появилось и стало развиваться промышленное производство гидравлических прессов для получения вина и оливкового масла, а позднее и для других целей.
Постепенно рядом с цехами компании Marzola (получившей название, подобно Biele, сложением частей фамилий двух ее основателей: Марродан и Резола), сфомировалась целая промзона из предприятий разных отраслей промышленности.
С середины ХХ века завод расширил ассортимент продукции и начал выпускать прессы для промышленного применения – гнутья железа, штамповки и пр. Однако до сих пор предприятие изготавливает винные прессы трех типов, пользующиеся стабильным спросом, – надежность техники под маркой Marzola за полтора столетия стала известна всей Европе. И не только.
Marzola идеально влилась в группу компаний Biele, поскольку философия двух бизнесов схожая: они разрабатывают инженерные проекты заказчиков с нуля и реализуют их «под ключ» по индивидуальным заказам. Оба во главу угла всегда ставят эффективность и высокую производительность выпускаемого оборудования, его бескомпромиссное качество.
Справка
Завод Biele в г. Аспейтиа, провинция Гипускоа
Площадь офисов – 2300 м2 Производственные цеха – 10 500 м2
Общая площадь – 42 000 м2
Взаимоотношения компаний строятся следующим образом: на заводе Marzola осуществляется проектирование, сборка, сервис, гарантийное обслуживание, но службы продаж и закупок обоих производств работают в Biele. Управление всеми подразделениями компании также осуществляется централизованно из штаб-квартиры Biele. Фактически Marzola – это второй цех Biele... в 150 км от первого.
В этом году запланирована модернизация производства. Основной производственный корпус и вспомогательные помещения будут оформлены в едином дизайне Biele Group. Получат дополнительные помещения проектировщики и программисты (офисное пространство увеличится вдвое). Большая территория завода позволяет построить новый цех – и эту работу тоже начнут в текущем году. Расширение позволит нанять новый персонал в дополнение к 60–70 сотрудникам, работающим здесь сейчас, а также ускорить сроки выпуска оборудования. Сегодня, в зависимости от сложности проекта и загруженности производства, срок исполнения заказа составляет от 6–7 до 10–12 месяцев (обычно около восьми).
«Нормальный для европейских клиентов срок ожидания готовности и поставки оборудования Biele может быть до полутора лет, – поясняет Сергей Зориков. – Но мы понимаем, что в России такое не работает, у нас все и всегда „нужно вчера“, поэтому мы стараемся подходить к нуждам российских клиентов наиболее гибко, зачастую сокращая период поставки до 7–9 месяцев.
Впрочем, есть виды оборудования, с которыми ускориться не получится, например, фанерные прессы: после изготовления пресс необходимо полностью собрать на заводе, подключить и протестировать, а потом разобрать перед отправкой клиенту – только эти операции занимают около двух месяцев. Люди относятся к этому с пониманием, тут важно лучше планировать свое будущее развитие и потребности».
Прессовое оборудование успешно решает чрезвычайно актуальную сегодня задачу: компоновку и соединение разнородных материалов, приобретающих при этом новые функциональные свойства. В последние десятилетия производство композитных материалов развивается особенно бурно. Стали возможны комбинации материалов, никогда ранее не доступные в промышленности – самые неожиданные сочетания, по желанию заказчика. Что особенно важно, для их производства необходимо высокоскоростное и мощное оборудование, ведь заказчиками подобных проектов выступают крупные компании, ориентированные на высокую продуктивность. Ключевым элементом новых технологий является пресс, поэтому Marzola и была интегрирована в компанию Biele. Комбинация возможностей двух компаний позволяет выпускать самые современные комплексные промышленные системы: быстрые, производительные, интеллектуальные и при этом почти не требующие участия человека.
Помимо собственно прессов, Marzola изготавливает также средства пристаночной механизации: гидравлическое оборудование, подъемные столы, толкатели, различные переворотные устройства, часто используемые при установке прессов в цехах. Сервисное обслуживание оборудование и управление проектами осуществляется из штаб-квартиры Biele, а проектирование, программирование и основное производство станков – здесь. За панорамным стеклом – технический офис. Там ведется подготовка предложений, разработка проектов.
Сборочная линия. Рядом со складом комплектующих и запчастей обращают на себя внимание три полностью готовые установки, которые тестируют перед отправкой заказчикам, а также целая шеренга винных прессов трех типов, которые компания продолжает с успехом выпускать и продавать по всему миру – от Италии и Германии до Китая и США. И это примерно 2% бизнеса Biele Group.
У транспортных ворот группируются материалы и составные части, которые в дальнейшем отправляются на монтаж линий.
А вот два еще не полностью собранных пресса: один для производства фанеры, другой – для HPL. За ними две станины, на которые будет установлено оборудование впоследствии. По соседству тяжелый 3000-тонный пресс с четырьмя гидроцилиндрами для производства резиновых изделий, используемых в соединениях трубопроводов (вес каждого такого изделия достигает 200 кг!). Пресс установлен в двухметровой глубины яме для испытаний, к нему подсоединены электрошкаф, гидростанция – все готово к включению!
Оставшуюся часть цеха занимает огромное «сердце» линии непрерывного действия для изготовления HPL прессованием высокого давления (90 кг/см3): 20-этажный пресс (восемь гидроцилиндров) с системами загрузки и выгрузки. Проведя испытания после сборки, завершив вместе с клиентом процедуру приемки оборудования, работники завода приступили к его разборке и упаковке отдельных частей для отправки потребителю. Для оборудования тяжелого класса на предприятии организована вторая яма, семиметровая, полностью оснащенная – в ней тестируются большие многопролетные прессы. Эта линия полностью автоматизирована, обслуживается одним человеком, работающим в зоне загрузки. Установка впечатляет своими размерами!
Здесь же можно видеть гидравлические системы, обеспечивающие работу как самого пресса, так и вспомогательного оборудования. Вся гидравлика проектируется, разрабатывается и изготавливается силами сотрудников Biele.
«Многие удивляются, насколько разнообразны наши проекты. Но в том-то и особенность, и сила наших компетенций, что мы способны воплощать самые смелые замыслы любого производителя, идет ли речь об обработке металла, древесины или, допустим, пластика. И у этих разработок нет почти ничего общего, кроме того, что все они созданы Biele, – говорит Андони Эриарте. – Такая персонализация процессов – дело, безусловно, недешевое. Но затраты полностью оправдываются, ведь мы способны предложить то, что другие не предлагают. Сейчас такое время, когда большинство компаний делают ставку на массовое производство, ориентированное на большие объемы, но не на конкретные нужды бизнеса. Им просто неинтересно заниматься индивидуальными решениями, поскольку это дорого не только для клиента, но и для разработчика. Благодаря своей мультисекторности Biele занимает в отрасли особую нишу. С момента основания мы инжиниринговая компания в полном смысле слова. Мы не из тех, кто просто делает и продает станки. Наши инженеры готовят базовую версию технологического решения, мы полностью разрабатываем технологическую цепочку, потом она „обставляется железом“ и далее дорабатывается для максимально точного и полного соответствия запросам клиента. Это всякий раз на 100% индивидуально разработанный продукт, который всегда доводится до совершенства при участии заказчика».
Справка
Завод Marzola в Наваррете:
Площадь офисов – 600 м2
Производственные помещения – 10 000 м2
Общая площадь завода – 42 000 м2
Было – и будет
Список проектов, реализованных Biele Group за последние годы, может занять много страниц, но нас, разумеется, интересуют главным образом производственные линии для деревообрабатывающих, плитных, мебельных производств.
Заключен договор на создание автоматизации для линии окрашивания на заводе Kronospan в Польше; линия прессования березовой фанеры создается для Estonian Plywood. Для известного испанского производителя плит (ДСП, MDF) Tableros Losan, пожелавшего выйти на рынок фанеры, полностью разработана технологическая оснастка – проект включал все производственные этапы: клеенанесение, прессование, обрезку, шлифование, упаковку... Среди недавних проектов также четыре упаковочные линии для мебельных фабрик в США.
Еще один крупный клиент – компания Lana, на чешском предприятии которой делают строительную опалубку. На поставленной туда линии в автоматическом режиме прессуется трехслойная доска и производится двутавровая балка из древесины.
Стоит упомянуть и линию для завода UPM в Эстонии. UPM Otepää Plywood Mill – фактически модельное предприятие, на которое любят приезжать деревообработчики из соседних регионов и стран, чтобы познакомиться с самым передовым оборудованием и общей организацией производственного процесса.
IKEA, очень крупный и важный клиент Biele, каждый год заказывает оборудование для своих предприятий. Последний контракт мегаконцерна включал автоматическую упаковочную линию: продукция упаковывается в коробки, коробки закрываются, наносятся этикетки, коробки ставятся на палеты и готовы к отгрузке. «Долговременное сотрудничество с IKEA дает уникальный опыт, – считает Андони Ириарте. – Запросы клиента бывают настолько необычные, что специально под них мы разрабатываем и создаем прототипы новых видов оборудования, о каких прежде и не задумывались и которые в дальнейшем становятся основой для других проектов. Очень сложные и вместе с тем куражные задачи. Так, например, по заказу IKEA была создана система, позволяющая определять качество поверхностей до покраски и отсортировывать качественные полуфабрикаты от некачественных, которые сразу уходят на переработку.
Латвийская компания VMG Industry, являющаяся поставщиком IKEA, приобрела линию покраски. Производство высокопроизводительное, системы автоматизации для таких скоростей способны делать единичные предприятия в мире. Поставка включала автоматические загрузку и выгрузку линии основной производственной линии, а также ту самую систему дефектоскопии, отделяющую качественные детали, поступающие на покраску, от бракованных. Она основана на «искусственном зрении». На вход в линию покраски с маленьким интервалом подается по несколько деталей в ряд. Специальные видеокамеры оперативно анализируют поверхность поступающих деталей, информация с них поступает в компьютер, который определяет бракованные детали и принимает решение об их удалении с конвейера и замещении качественными. Необходимо, чтобы пачка на выходе была полной и ровной, а все детали – только определенного качества. Роботизированный загрузчик позволяет делать до 30 рабочих циклов в минуту. Бракованные детали отдельный транспортер перемещает на вторичную переработку.
Для уругвайского производителя фанеры Uruply создана роботизированная линия для автоматического ремонта листов фанеры: набор сканеров в проходном режиме определяет место и характер дефекта, компьютер обрабатывает полученную информацию и на ее основании формирует для системы задание по оптимизации: где и как вырезать некачественный фрагмент, чем заполнить, нужно ли добавить в пасту полиуретан, необходимы ли фрезерование, шлифовка. Линия способна ремонтировать до 25 панелей в минуту, работая в непрерывном режиме: круглосуточно семь дней в неделю. Если прежде на предприятии устранением дефектов занимались огромное количество работников – 220 человек, то теперь машины могут делать это сами.
По заказу финской компании UPM разработаны и построены два уникальных пресса для удаления влаги из шпона в фанерном производстве. Особая новая технология Biele позволяет достичь равномерного распределения влаги внутри пачки шпона, удалить ее излишки без повреждения материала и тем самым снизить расходы на сушку. Эти установки – единственные в мире с подобной технологией, которые по-настоящему работают.
Знают испанское оборудование и в Беларуси, оно работает на предприятии «Бобруйскмебель» и скоро будет пущено на VMG в Могилеве – контракт был заключен в 2018 году, в настоящее время идет монтаж конвейеров для заказанной линии упаковки.
Первым проектом Biele в России стала поставка короткотактного пресса для облицовки ДСП в Смоленск, на мебельное предприятие «Смоленскмебель», (работает по заказам ИКЕА) в 2008 году. Пресс бесперебойно работает по сей день. За этим контрактом последовали поставки автопроизводителям – заводы в Калуге (Volkswagen) и Нижнем Новгороде были оснащены прессами для изготовления элементов внутренней отделки и изоляции автомобилей.
Самым большим проектом, реализованным Biele в деревообрабатывающей отрасли России, стали поставки на завод IKEA. Сейчас оборудование Biele работает в Великом Новгороде и Нижнем Новгороде, Санкт-Петербурге и Москве...
Наша марка в России известна, но я прекрасно понимаю, насколько велика ваша страна, как много крупных заводов в разных ее уголках. Если наша встреча поможет российским производителям лучше познакомиться с машиностроителями из Страны Басков, а наша компания станет им ближе, я буду рад и горд«.
Без компромиссов
Перфекционизм, заложенный в слогане Dream More, неустанное стремление к лучшему из возможного (или даже: к лучшему, чем возможно) определяет деятельность компании во всех ее проявлениях. «Качество – во всем», – так рассуждают и руководители, и рядовые работники Biele, в повседневной работе следующие жестким правилам ежегодно подтверждаемых сертификатов ISO9001:2000, ISO14001. На предприятиях Biele действует программа постоянного совершенствования, подобная той бизнес-модели, что существует, например, на заводах Toyota. И касается это не только производства продукции, ее конструкции и дизайна, но и послепродажного обслуживания.
Высочайший уровень автоматизации оборудования зачастую предусматривает лишь одного специалиста для обслуживания целой линии, но при этом речь идет больше, чем о простом операторе: это в своем роде начальник линии, работа которого основана на профессиональных знаниях и компетенции; он осуществляет контроль всего процесса в целом.
«Служба сервиса и технической поддержки ввиду сложности технологических линий, которые мы производим, работает в круглосуточном режиме: клиент в любое время может позвонить и получить необходимую консультацию и помощь, – говорит Сергей Зориков. – Гарантия на наше оборудование складывается из нескольких составляющих. По части механики в стандартном варианте она составляет один год (если необходимо, продлевается до двух или даже трех лет, в зависимости от условий проекта). При этом очень важно, что, предоставляя годичную гарантию, мы рассчитываем, что линия будет работать без остановки целый год, то есть 365 дней круглосуточно. Кроме того, мы несем гарантийные обязательства по производительности нашей техники: показатели, заявленные в проекте, должны быть обеспечены в течение всего срока эксплуатации.
Комплексный проект в числе прочих возможностей постпродажного сервиса предполагает еще и круглосуточную телефонную поддержку: когда бы вы ни обратились в колл-центр Biele с возникшей проблемой, квалифицированный специалист будет на связи и поможет оперативно ее решить».
В России у испанского производителя есть компания-партнер «Спутник» (Санкт-Петербург), которая берет на себя монтажные функции, если в соглашении с клиентом оговорен не шеф-монтаж, а полный монтаж от производителя. Эта, а также другие подрядные организации, могут быть привлечены и для обслуживания оборудования. А вот инженеры-электронщики и программисты – только собственные. Они готовы при необходимости в любой момент выехать на предприятие клиента, но чаще всего их квалификация позволяет решить все сервисные вопросы удаленно. «Все-таки главное, на чем компания зарабатывает деньги, – это прежде всего инженерия, интеллектуальный труд и глубочайшее знание своего дела», – с гордостью подчеркивает Андони Ириарте.
Жизненный цикл проекта в Biele описывает Сергей Зориков: «Клиент приходит и говорит: мне нужно из такого-то сырья произвести такой-то продукт с такими-то параметрами и в таких-то объемах. Мы задаем ему возникшие по ходу изучения ТЗ уточняющие вопросы, чтобы понять серьезность намерений и выяснить, знает ли человек, чего он хочет». Первичное техническое решение обычно готовится в нескольких (бывает и до 20!) версиях, всесторонне обсуждается и согласовывается с заказчиком, только после этого начинается воплощение чертежей и моделей в реальную технологическую линию.
«Как бы мы ни старались идти навстречу клиенту в желании сэкономить, есть пределы, ниже которых „упасть“ не можем, поскольку категорически не готовы экономить на материалах, комплектующих и прочем, – поясняет Сергей Зориков. – Наши заказчики понимают и ценят это стремление компании неукоснительно придерживаться самых высоких стандартов качества. Понимают они и еще одну важную вещь: то, что заказывают у нас, они попросту не смогут получить нигде больше. В Европе крайне мало таких разноплановых и гибких машиностроительных предприятий, способных, а самое главное – готовых взяться за нестандартные, индивидуальные, порой в буквальном смысле уникальные промышленные проекты. А для Biele нет нерешаемых задач».
«У вас есть проблема? У нас есть решение!» – так могли бы выразить свое кредо специалисты Biele. Если бы они были волшебниками. Но Сергей Зориков сугубый реалист: «Все так и было бы, если задача точно и правильно определена. Главная проблема, с которой мы сталкиваемся, это неопределенность желаний клиента. Казалось бы, бизнес, высокие технологии, большие инвестиции – но сколько раз приходилось сталкиваться с „техническими заданиями“ вроде: как бы так сделать, чтобы ничего не делать, – а прибыль получать? Чем точнее заказчик представляет и ставит задачу, тем более адекватным его запросам окажется результат нашей совместной работы».
«Мы можем решить любую проблему клиента, – говорит Андони Ириарте. – Главное, чтобы заказчик грамотно ее сформулировал: что, как, откуда, куда. Если он способен ответить на эти вопросы применительно к планируемому производству, значит, понимает, чего хочет, тогда нам останется приложить все усилия, чтобы ему помочь. Нас ведет вперед стремление к постоянному самосовершенствованию, и это как нельзя лучше соотносится с инженерным подходом к проектам, когда мы каждый раз все начинаем с нуля, с самого начала...»
Текст и фото Максим Пирус