Особенности углового пиления
В настоящее время на рынке лесопильного оборудования России довольно много предложений о продаже углового лесопильного оборудования производства разных компаний, которое различается по конструкции, установленной мощности и уровню оснащенности разного рода механизацией. Знакомясь с подобными предложениями, невольно отмечаешь, что производители конструктивно разных станков, цены на которые различаются в несколько раз, дружно обещают покупателям удивительно высокую производительность оборудования. Автор этой публикации попытается разобраться, где правда.
Во-первых, следует определиться с терминами. Словосочетание «угловая лесорама» не имеет права на существование, т. к. слово «лесорама» (лесопильная рама) относится к оборудованию, в котором используется возвратно-поступательное движение режущего инструмента, так называемых полосовых пил, установленных в пильной рамке. Углопильное же оборудование оснащено только круглыми пилами и, следовательно, представляет собой в основе бревнопильный круглопильный станок. В зависимости от оснащения режущим инструментом, т. е. от количества установленных на нем круглых пил, и конструктивных особенностей (например, наличия поворотного пильного шпинделя или двух взаимно перпендикулярно установленных шпинделей), подобные станки могут быть однопильными и многопильными.
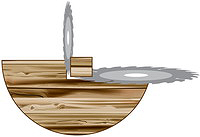
Рис. 1. Схема работы углопильного
бревнопильного станка
Принципиальная схема работы углового станка представлена на рис. 1.
Первыми на российском рынке подобное оборудование в конце 90-х годов прошлого века представили две фирмы – из США и Словакии. Лесопильный станок «Гризли» изготавливается американской фирмой LMCA Ltd более 45 лет и с 1995 года по лицензии изготавливался в России на ЗАО «Агропромсервис», а затем, с 2000 года, – на его дочернем предприятии ООО «ПГ "Гризли"».
Словацкая фирма StrojCAD s.r.o. производит с 1990-х годов однодисковые станки UH 500 и UP 700 для радиального раскроя, двухдисковые станки КР 58 (аналоги которых в последнее время начали выпускать и в России), а также оборудование для заточки разных типов пил.
Сейчас только в нашей стране производителей подобного оборудования больше пятидесяти, они выпускают оборудование разных конструкций и ценовых категорий – от 200 тыс. до 3,0 млн руб., разной производительности, степени механизации и автоматизации.
Станки с угловым пилением, представленные на российском рынке, можно разделить на три группы:
- двухпильные с подвижным бревном и неподвижным пильным порталом;
- двухпильные со стационарно закрепляемым бревном и подвижным пильным порталом;
- с поворотным пильным диском на подвижном портале и со стационарно закрепляемым бревном.
Наибольшее распространение в настоящее время получили станки двухпильные со стационарно закрепляемым бревном, т. к. их установка позволяет значительно экономить площадь, механизировать и автоматизировать процессы загрузки, разгрузки сырья и пиломатериалов, а также установку и зажим бревна. Кроме того, конструкция этого оборудования позволяет легко встраивать его в поточную линию, состоящую из нескольких станков.
Производительность оборудования
Двухпильные станки универсальны, и их целесообразно применять для получения специфицированных пиломатериалов радиального и тангентального раскроя (которые используются, например, для производства музыкальных инструментов, оконных трехслойных брусков или паркета), а также для изготовления деталей для домостроения и погонажа на предприятиях с объемами производства пиломатериалов не менее 500–600 м3 в месяц при организации работы в две смены. Подобное оборудование может также применяться на лесопильных производствах для переработки толстомерного пиловочного сырья (диаметром более 66 см) в объеме 1–5% общего объема перерабатываемого сырья.
Для обеспечения коммерчески выгодного (рентабельного) лесопиления на подобном оборудовании необходимо обеспечить высокое качество и необходимые параметры перерабатываемого сырья. Наиболее целесообразно для получения специфицированных и специальных пиломатериалов пилить бревна только 1-го и 2-го сорта диаметром не менее 32 см. Если таких условий нет, то тогда нужно продумать другие технологические схемы раскроя, использовать вместе с угловыми станками оборудование другого типа, разделение потоков по диаметру распиливаемого сырья. Заметим также, что угловые станки производительностью 2–3 м3 в смену в основном предназначены для небольших частных производств и фермерских хозяйств с целью обеспечения потребности в пиломатериалах и в этой публикации не рассматриваются.
Производительность двухпильных станков зависит от диаметра и длины распиливаемых бревен, способа загрузки бревна и съема остаточного горбыля, установленной мощности привода пильных суппортов и механизма подачи, от конструктивных особенностей станка (механизмов загрузки, установки и крепления бревен, перемещения пильных суппортов и других факторов). Подобное оборудование относится к разряду циклопроходного, и, как показывает опыт автора, а также данные некоторых производителей, основная часть рабочего цикла раскроя бревна на пиломатериалы приходится на процесс пиления. Так, например, при раскрое бревен диаметром 36–38 см и длиной 4 м на радиальные пиломатериалы сечением 27 х 97 мм (для производства оконного трехслойного бруса) с загрузкой бревна на станок с помощью тельфера и ручным зажимом на станке продолжительность полного цикла может составлять 13–15 мин. Причем 75% этого времени приходится на пиление, 20% – на загрузку и установку бревна на станке, 5% – на съем оставшегося горбыля. Эти цифры могут незначительно меняться в зависимости от выпиливаемого сечения пиломатериалов, установленной мощности привода и конструктивных особенностей оборудования, но в любом случае на операцию пиления приходится наибольший отрезок рабочего цикла раскроя бревна.
Рассмотрим все стадии и нюансы цикла пиления подробно.
Хочется сразу отметить, что для обеспечения высокой эффективности пиления наиболее желателен такой цикл, в котором реализуется возможность пиления бревна при обратном ходе каретки станка, а также возможность автоматического сброса отделенного от бревна пиломатериала (доски) и горбыля. К сожалению, автору статьи неизвестны станки с конструкцией, позволяющей одновременно автоматически выполнять такие операции.
На практике при раскрое бревна во время обратного хода каретки станка сброс доски и позиционирование суппортов осуществляются параллельно оператором и вспомогательным рабочим. Для обеспечения высокой производительности целесообразно задействовать двух подсобных рабочих: для съема пиломатериала с обоих торцов бревна и удаления горбыля и срезок из зоны пиления.
Понятно, что оснащение станка системой автоматического позиционирования бревна и пильных суппортов значительно сокращает фактическое время пиления бревна на пиломатериалы по сравнению с пилением на станке с ручным позиционированием пильных суппортов. Особенно когда речь идет о начале процесса пиления, т. к. при ручном позиционировании оператору требуется время на то, чтобы визуально «пристреляться» к требуемому положению пильных дисков и их дальнейшему позиционированию при каждом последующем резе. Автоматизация позиционирования может повысить производительность оборудования на 10–12%, а это весьма существенно.
При использовании станка с автоматическим программированием процесса пиления так называемый человеческий фактор, по сути, не оказывает влияния на производительность оборудования. Кроме того, нужно учитывать, что время, необходимое для полного цикла распиловки бревна, включает время, требуемое для установки бревна и съема остаточного горбыля, и оно может составлять до 25% общего времени цикла распиловки. Поэтому реальный выигрыш в производительности при создании условий для реализации процесса пиления при обратном ходе каретки станка может составить не более 20–25%. В условиях реального производства эти показатели могут иметь существенное значение, особенно если учесть не очень высокую рентабельность большинства лесопильных производств.
Имеет смысл детально разобраться с особенностями процесса пиления при обратном ходе каретки станка, это позволит осознанно подходить к выбору того или иного способа пиления.
Вот некоторые из этих нюансов:
- необходимо задействовать дополнительный персонал для съема пиломатериала с обоих торцов бревна;
- в процессе пиления при обратном ходе каретки в первую очередь в бревно врезается вертикальная круглая пила, поэтому при горизонтальном выпиливании досок в конце пиления, когда вертикальная пила уже выходит из тела бревна, широкая пласть доски остается лежать на горизонтальной круглой пиле, что может привести к неконтролируемому сколу (вырыву) и даже выбрасыванию доски из-под пил (на вертикальных однопильных бревнопильных лентах); существуют механизмы поддержки отпиливаемой доски, например роликом, что уменьшает или полностью снимает проблему скола на конце доски и оставшейся в зажимах части бревна.
- пиление горизонтально расположенных широких досок (более 150 мм) может быть опасным для персонала. При вертикальном расположении доски вероятность выброса существенно ниже из-за уменьшения зоны контакта кромки доски с горизонтальной пилой, но все же она существует.
При пилении широких или тяжелых пиломатериалов для обеспечения нормального пиления, без зажима круглых пил, горизонтальной пиле производители оборудования обычно придают некоторый наклон в направлении пиления (создают угол между плоскостью пиления и плоскостью тела пилы, т. е. обеспечивают так называемый угол атаки). В процессе пиления при обратном ходе каретки горизонтальная круглая пила будет входить в тело бревна с отрицательным углом атаки, поэтому нагрузка на пильный диск будет неоптимальной. При наличии угла атаки (как правило, не более 0,5°) при входе пилы в бревно на пилу начинает действовать дополнительная боковая составляющая силы, которая при стремлении пилы занять устойчивое положение пилы в пропиле повысит ее жесткость и устойчивость. Также она будет неоптимальная и при полном отсутствии угла атаки. В итоге отсутствие угла атаки может способствовать ускоренному износу зубьев и тела пилы, а иногда даже и ее зажиму в пропиле и подгоранию и образованию прижогов на теле пилы, что приведет к ее выходу из строя. По этой причине выпиливание горизонтальных досок с широким сечением, особенно из тяжелой (твердой) древесины, при обратном ходе каретки может оказаться проблематичным. Следует отметить также, что на фрезерно-брусующих линиях со скоростью подачи свыше 70 м/мин. угол атаки не превышает 0,5°, а при пилении на угловых станках толстых и широких пиломатериалов, как правило, не более 240 мм, и на скорости подачи не более 30 м/мин. угол может быть 0,2–0,3°. Такой угол атаки применяется на оборудовании только в том случае, когда надо компенсировать проблемы недостаточно жестких дешевых пил и повысить их жесткость и устойчивость в пропиле за счет создания угла атаки, т. е. с помощью конструктивных особенностей оборудования. При использовании для пиления пилы с повышенными характеристиками (высококачественная сталь корпуса и выполненные на высоком уровне термообработка и вальцовка) создание угла атаки на угловых станках можно исключить, что приведет к повышению производительности оборудования за счет применения пиления при использовании обратного хода каретки. Поэтому не экономьте на режущем инструменте, оборудовании, механизации и автоматизации, если вас интересует экономическая целесообразность углового пиления.
Почти на всех углопильных станках используется встречная подача (когда вектор скорости вращения пильного диска направлен навстречу вектору скорости подачи), т. к. при такой подаче невозможен самопроизвольный встречный выброс пиломатериала. Попутная подача, которая будет иметь место при пилении вместо холостого хода, допускается только на станках с механической (а не ручной) подачей и на оборудовании с когтевой защитой, препятствующей выбросу пиломатериала. Однако учитывая тот факт, что усилия резания на углопильных станках, как правило, не превышают силы трения скольжения между отпиленной доской и частью бревна даже у пиломатериалов небольшого сечения, можно утверждать, что самопроизвольного выброса пиломатериала при пилении на обратном ходу каретки и при попутной подаче в этом случае не будет.
Следует отметить, что наиболее подходящие условия для использования обратного пиления обеспечиваются, когда одновременно:
- распиливаются бревна мягких пород древесины (кроме осины и липы);
- раскраиваются окоренные бревна или с чистой, незагрязненной, поверхностью;
- горизонтальным пильным диском осуществляется неглубокий пропил (не более 70 мм), т. е. выпиливаются либо вертикально расположенные широкие и толстые доски, либо рейки небольшого сечения.
Что касается времени, необходимого для установки бревна на станок и съема остаточного горбыля со станка, то оно сильно зависит от видов используемых механизмов для загрузки бревна, выравнивания бревна и от конструкции зажимов. Например, использование механизма поштучной подачи бревен в совокупности с гидравлической системой для выравнивания и зажима бревна, а также гидравлической системой сброса остаточного горбыля, устройством аспирации для удаления мягких отходов из зоны резания обеспечивает сокращение этого отрезка времени почти в два раза по сравнению с отрезком времени, необходимым для загрузки бревна тельфером и использования механических зажимов с ручным выравниванием бревна.
Большую роль в обеспечении производительности оборудования и увеличении объемного выхода пиломатериалов играет правильный выбор режущего инструмента, в том числе и круглых пил. Например, применение тонких пил позволит увеличить скорость подачи и, как следствие, производительность оборудования, уменьшить отпад древесины в кусковые отходы и опилки, снизить потребление электроэнергии, увеличить объемный выход пиломатериалов. Сейчас почти на всех станках используют пилы диаметром от 400 до 600 мм. Для того чтобы увеличить объемный выход пиломатериалов, когда вы пилите пиломатериалы сечением не больше 100 х 100 мм, целесообразнее всего использовать пилы диаметром не более 400 мм, а при пилении пиломатериалов, например, сечением не больше 200 х 200 мм целесообразнее использовать пилы диаметром 600 мм или применять какую–либо другую комбинацию, при которой необязательно использование пил одинакового диаметра.
Применение круглых пил с минимально допустимым количеством зубьев и требуемым качеством пиленой поверхности (не более Rz320) позволит снизить удельные силы резания при пилении и повысить скорость подачи при прочих одинаковых условиях (при минимально допустимом количестве зубьев снижаются удельные силы резания, потребляемая мощность оборудования, что позволяет при всех прочих одинаковых показателях увеличить скорость подачи, а следовательно и производительность оборудования).
Факторы выбора мощности привода шпинделя
На примере пил диаметром 550 мм разных производителей – пилы 550 х 4,8/3,4, z = 24 + 2 + 2 + 2, производства компании AKE, и пилы 550 х 5,5/3,5, z = 18+6, производства компании GASS – рассмотрим степень влияния количества зубьев, ширины пропила, агрегатного состояния древесины разных пород, степени затупления режущих кромок зубьев пил на потребляемую мощность привода механизма резания и, как следствие, на реально достижимую производительность оборудования. В качестве исходного пиломатериала примем пиловочник трех пород: сосны, лиственницы и дуба влажностью 45–75% с агрегатным состоянием древесины (талая и мороженая) и влиянием степени затупления лезвия зубьев пилы (острая – тупая). Условно пилим заготовки для клееного оконного бруса сечением 30 х 100 мм (с учетом усушки), сердцевину бревна на брус сечением 100 х 100 мм (без учета усушки); для увеличения объемного выхода из некондиционной части бревна пилим рейки сечением 30 х 50 мм, например, для производства плинтуса. Для расчетов примем частоту вращения круглых пил, установленных по одной на валу асинхронного двигателя, 2940 об./мин. Для определения максимального значения установленного электродвигателя одного из пильных шпинделей расчеты проведем для наихудших условий пиления.
Зная, что для процесса пиления с хорошим качеством пиления получаемых поверхностей пиломатериалов минимальная подача на зуб (uz) должна быть не менее 0,3 мм, средняя – 0,6 мм, максимальная – 1,0 мм, можем подсчитать скорость подачи для пил с 18 и 24 зубьями по формуле
u = uz х z х n/(60 х 1000), (1)
где: uz – подача на зуб, мм, z - число зубьев на пиле, шт., n – частота вращения пилы в пропиле, об./мин.
Все расчеты выполнены по одному шпинделю (по второму аналогично) и сведены в табл. 1.
допустимой подачи на зуб и количества зубьев на пиле при
продольном пилении
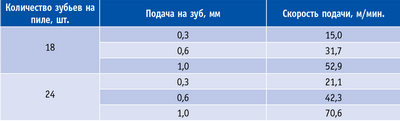
Анализируя данные, представленные в табл. 1, можно сделать вывод: при одинаковой подаче на зуб и одинаковом качестве (шероховатости) получаемой поверхности желательно использовать пилы с 24 зубьями, т. к. скорость подачи при этом может быть выше, чем при использовании пилы с 18 зубьями, а производительность станка, оснащенного пилой с таким количеством зубьев, выше, чем станка с пилой, у которой 18 зубьев.
Мощность привода пильного шпинделя рассчитывается по формуле, кВт:
Nрез. = αпопрKтBHiu/60, (2)
где αпопр – поправочный коэффициент для продольного пиления круглыми пилами; Kт – табличное значение удельной силы резания, Дж/см3; B – ширина пропила, мм; H – высота пропила, м; i - количество пил на шпинделе, шт.; u – скорость подачи, м/мин.
Поправочный коэффициент для продольного пиления круглыми пилами рассчитывается по формуле
αпопр = αп αw αp ασ αv αh αt, (3)
где αп – поправочный коэффициент на породу (сосна – 1,0; лиственница – 1,1; дуб – 1,55); αw – поправочный коэффициент на влажность древесины, для сырой древесины (W = 45–75%) – 1,0; αp – поправочный коэффициент на затупление лезвия зуба в процессе работы пилы (0 ч – 1,0, 3 ч – 1,8, 6 ч – 2,8); ασ – поправочный коэффициент на угол резания (например, при σ = 75° α σ = 1,55, а при σ = 65° ασ = 1,16); αv – поправочный коэффициент на скорость резания, который равен 1,18 при Vср, вычисленной по формуле, м/с:
Vср = π х D х n / (60 х 1000), (4)
где π = 3,14; D – диаметр пилы, мм; n – частота вращения пилы, об./м; Vср = 3,14 × 550 × 2940)/(60 × 1000) = 84,6 м/с; ah – поправочный коэффициент, учитывающий высоту пропила, мм, при H = 100 мм ah = 1,2; αt – поправочный коэффициент на агрегатное состояние древесины (талая древесина при плюсовой температуре окружающего воздуха – 1,0, мороженая – 2,0).
Итак, для талой древесины сосны αпопр = 1,0 х 1,0 х 1,0 х 1,16 х 1,18 х 1,2 х 1,0 = 1,6; для мороженой αпопр = 1,0 х 1,0 х 1,0 х 1,16 х 1,18 х 1,2 х 2,0 = 3,2;
для талой древесины лиственницы αпопр = 1,1 х 1,0 х 1,0 х 1,16 х 1,18 х 1,2 х 1,0 = 1,8, для мороженой αпопр = 1,1 х 1,0 х 1,0 х 1,16 х 1,18 х 1,2 х 2,0 = 3,6;
для талой древесины дуба αпопр = 1,55 х 1,0 х 1,0 х 1,16 х 1,18 х 1,2 х 1,0 = 2,5, для мороженой αпопр = 1,55 х 1,0 х 1,0 х 1,16 х 1,18 х 1,2 х 2,0 = 5,0.
Kт = 49,0 Дж/см3 при uz = 0,3 мм,
Kт = 40,5 Дж/см3 при uz = 0,6 мм;
Kт = 31,5 Дж/см3 при uz = 1,0 мм.
B – ширина пропила, мм, определяется по формуле
B = S + 2S¹, (5)
где S – толщина тела пилы, мм, 2S¹ – уширение зубьев на сторону, мм.
Для пилы производства АКЕ 550 х 4,8/3,4, z = 24 + 2 + 2 + 2: B = 3,4 + 2 х 0,7 = 4,8 мм.
Для пилы производства GASS 550 х 5,5/3,5, z = 24 + 6: B = 3,5 + 2 х 1,0 = 5,5 мм.
H – высота пропила, мм, Нрасч. = 0,1 м; i – количество пил на шпинделе, шт., i = 1 шт.; u – скорость подачи, м/мин., расчетные данные приведены в табл. 1.
Расчеты мощности привода пиления для пиломатериалов разных пород, агрегатного состояния, максимально допустимой скорости подачи и ширины пропила (для пилы GASS) при угле резания 65° и острых пилах (αр = 0 ч):
– сосна талая:
Nрез. = 1,6 х 31,5 х 5,5 х 0,1 х 1 х 52,9/60 = 24,4 кВт при uz = 1,0 мм;
Nрез. = 1,6 х 31,5 х 5,5 х 0,1 х 1 х 31,7/60 = 14,6 кВт при uz = 0,6 мм;
Nрез. = 1,6 х 31,5 х 5,5 х 0,1 х 1 х 15,0 / 60 = 6,9 кВт при uz = 0,3 мм;
– сосна мороженая:
Nрез. = 3,2 х 31,5 х 5,5 х 0,1 х 1 х 52,9/60 = 48,8 кВт при uz = 1,0 мм;
Nрез. = 3,2 х 31,5 х 5,5 х 0,1 х 1 х 31,7/60 = 29,2 кВт при uz = 0,6 мм;
Nрез. = 3,2 х 31,5 х 5,5 х 0,1 х 1 х 15,0 / 60 =13,8 кВт при uz = 0,3 мм.
Рассчитаем мощность привода пиления при пилении пиломатериалов тонкой пилой (при всех прочих одинаковых условиях) сосны талой (см. табл. 1).
Nрез. = 1,6 х 31,5 х 4,8 х 0,1 х 1 х 52,9/60 = 21,3 кВт при uz = 1,0 мм.
Таким образом, применение при пилении качественных тонких круглых пил может не только снизить отпад древесины в опилки, но и повысить производительность оборудования с увеличением расчетного выхода готовой продукции не менее чем на
3–5 %, как в приведенном выше расчетном примере.
Реальная рабочая скорость подачи будет 30–50 м/мин., т. е. подача на зуб не должна превышать 0,6 мм. При пилении лиственницы производительность оборудования вырастет на 12%, а при пилении пиломатериалов дуба – на 36%.
Выводы и рекомендации
- эффективность углового дискового пиления обрезных пиломатериалов выше, чем пиления с использованием ленточно-пильного и рамного оборудования;
- стоимость инструмента для угловых дисковых пилорам выше, чем инструмента для ленточных пилорам с узкими пилами, поэтому нужно учитывать качество входящего сырья, однако удельные расходы инструмента при круглопильном пилении в пересчете на 1 м3 пиломатериалов ниже (выводы из личного опыта и знания стоимости оборудования);
- на угловых станках рекомендуется распиливать бревна диаметром 360 мм и более, для бревен меньшего диаметра лучше использовать оборудование для развального или брусо-развального метода раскроя;
- для наиболее эффективного пиления и достижения высокой производительности на углопильных станках, как указывают производители, 8–10 м3 в смену обрезных пиломатериалов, особенно сосновых, сечением 30 х 100 мм, надо, чтобы у пильных шпинделей установленная мощность была не менее 22 кВт, а при пилении твердых пород или мороженой древесины – 40–50 кВт;
- при раскрое пиловочника на основные толстые и широкие пиломатериалы, включая материалы сечением 200 х 200 мм, производительность станка в смену по причине ограничения выпиливаемых из бревна досок большого сечения и сокращения общего количества пропилов может быть и больше, чем при раскрое пиломатериалов на доски небольшого сечения. Для увеличения производительности оборудования потребуется обязательная механизация погрузо-разгрузочных работ на станке, включая автоматизацию всех процессов на оборудовании;
- что касается максимального объемного выхода пиломатериалов, то он, как правило, не превышает 70% (а вовсе не 95%, как обещают отдельные производители оборудования). Ведь в общем балансе пиловочного сырья при раскрое его на пиломатериалы 6–7% приходится на усушку (т. к. следует пилить специфицированные пиломатериалы с припусками на усушку, а при поставках на экспорт и с плюсовыми припусками 1–3 мм на сторону), 12% – опилки, кусковые отходы (рейки, горбыль) – еще 8–10%. Подсчитать несложно.
Максимальный же выход радиальных пиломатериалов из общего объемного выхода и вовсе не превышает 60%, причем только при раскрое 1-го и 2-го сорта пиловочника диаметром не менее 36 см. Иными словами, выход кондиционных радиальных пиломатериалов при пилении на угловых станках не должен превышать 42% в общем объеме пиломатериалов, включая короткомерные (длиной до 0,8 м);
- применение при раскрое пиловочника качественных тонких круглых пил может снизить не только отпад древесины в опилки и тем самым повысить расчетный выход готовой продукции не менее чем на 3–5%, но также увеличить производительность оборудования за счет повышения скорости подачи при прочих равных условиях.
Владимир ПАДЕРИН